Researchers from several universities have unveiled a groundbreaking metamaterial that could transform the future of engineering. Designed with an innovative combination of materials, this new development exhibits the rare property of quasi-zero stiffness (QZS), allowing it to withstand significant loads while remaining nearly immune to vibrations. This could open the door to previously unimaginable applications in fields requiring both stability and flexibility, such as aerospace, construction, and precision manufacturing.
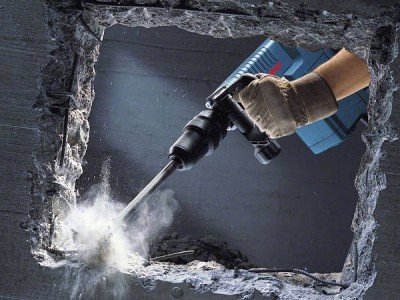
At the core of this advancement is a delicate balance between two opposing material properties: negative and positive stiffness. The material’s unique structure combines elements that are easily bent (negative stiffness) with components that resist bending (positive stiffness). The result is a dynamic material that can bear heavy loads yet suppress minor vibrations, offering an unparalleled level of stability.
The metamaterial’s intricate design features parallel cells composed of inclined and semicircular elements. This geometric configuration is key to achieving quasi-zero stiffness, a property that essentially enables the material to isolate vibrations while maintaining its load-bearing capacity. In environments where even the slightest vibration could compromise performance or safety—think of sensitive equipment in spacecraft, precision machinery, or high-rise buildings—this material could be a game changer.
Quasi-zero stiffness (QZS) is a rare state in which a material exhibits almost no resistance to small displacements, which makes it ideal for isolating vibrations without compromising its structural integrity. The ability to absorb vibrations while maintaining stress tolerance opens up numerous possibilities for industries that rely on precision, such as semiconductor manufacturing or medical equipment design, where the tiniest shake can disrupt processes.
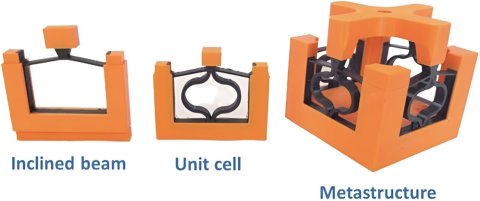
This metamaterial could revolutionize vibration-dampening technology across multiple sectors. In aerospace, for instance, where spacecraft and satellites are exposed to constant mechanical stress and unpredictable vibrations, the use of QZS material could enhance stability, leading to more reliable equipment. In construction, buildings in earthquake-prone regions could benefit from this material’s ability to flex under stress while protecting essential infrastructure from damage. Even the automotive industry could see improved vehicle designs, where minimizing engine vibrations and road impacts becomes easier and more efficient.
Moreover, the potential of this metamaterial extends to military and defense applications. Sensitive surveillance equipment, weapons systems, or mobile command centers, all of which operate in environments subject to vibrations and shocks, could achieve a new level of protection with QZS. Additionally, its ability to withstand extreme forces while maintaining equilibrium could have critical implications for disaster-resilient structures or rescue equipment.
As this new material moves from laboratory testing to practical deployment, it could pave the way for a wave of engineering solutions that were previously unachievable. From stabilizing towering skyscrapers to safeguarding delicate scientific instruments, the impact of QZS metamaterials may soon become a cornerstone of next-generation technology and design.